As the largest manufacturing centre for the Britvic group, the Rugby factory produces around half of the group’s soft drinks. With increased sales for popular brands, such as Pepsi, Fruit Shoots and J2O, manufacturing output needed to grow to fulfil this demand. Increasing the supply of the principal ingredient, purified water, was critical to meeting new targets. Only a holistic approach to this complex and challenging manufacturing environment could deliver results and set in motion a continuous improvement approach to water treatment and water purification solutions.
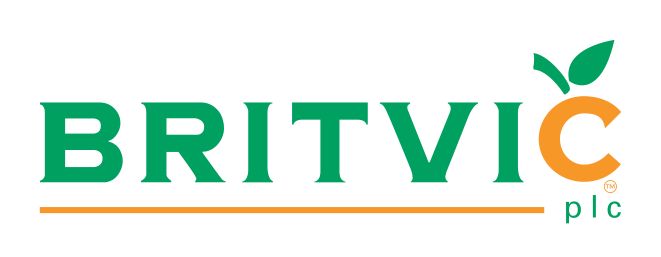
“The Envirogen Group has worked with Britvic for many years,” says Bill Denyer, European CEO at Envirogen Group. “As a major player in the soft drinks industry, their experience in production and their vision for future growth is second to none. We were thrilled to be able to help them achieve their manufacturing ambitions at their flagship UK site, which showcases the best of what Britvic has to offer. Britvic’s unique and complex water cycle, featuring fast production times, high volume purified water requirements, demanding environmental standards and sterile lines, requires the type of expert design and management that is our specialism.”
“High-quality purified water is the main ingredient in many of the Britvic products so the efficiency of the whole manufacturing process rests on the effectiveness of the water treatment process. The site already produced purified water at a rate of 200m³/hour, but to meet increased demand, Britvic knew that additional 160m³/hour, would need to be processed nearly doubling the existing supply.”
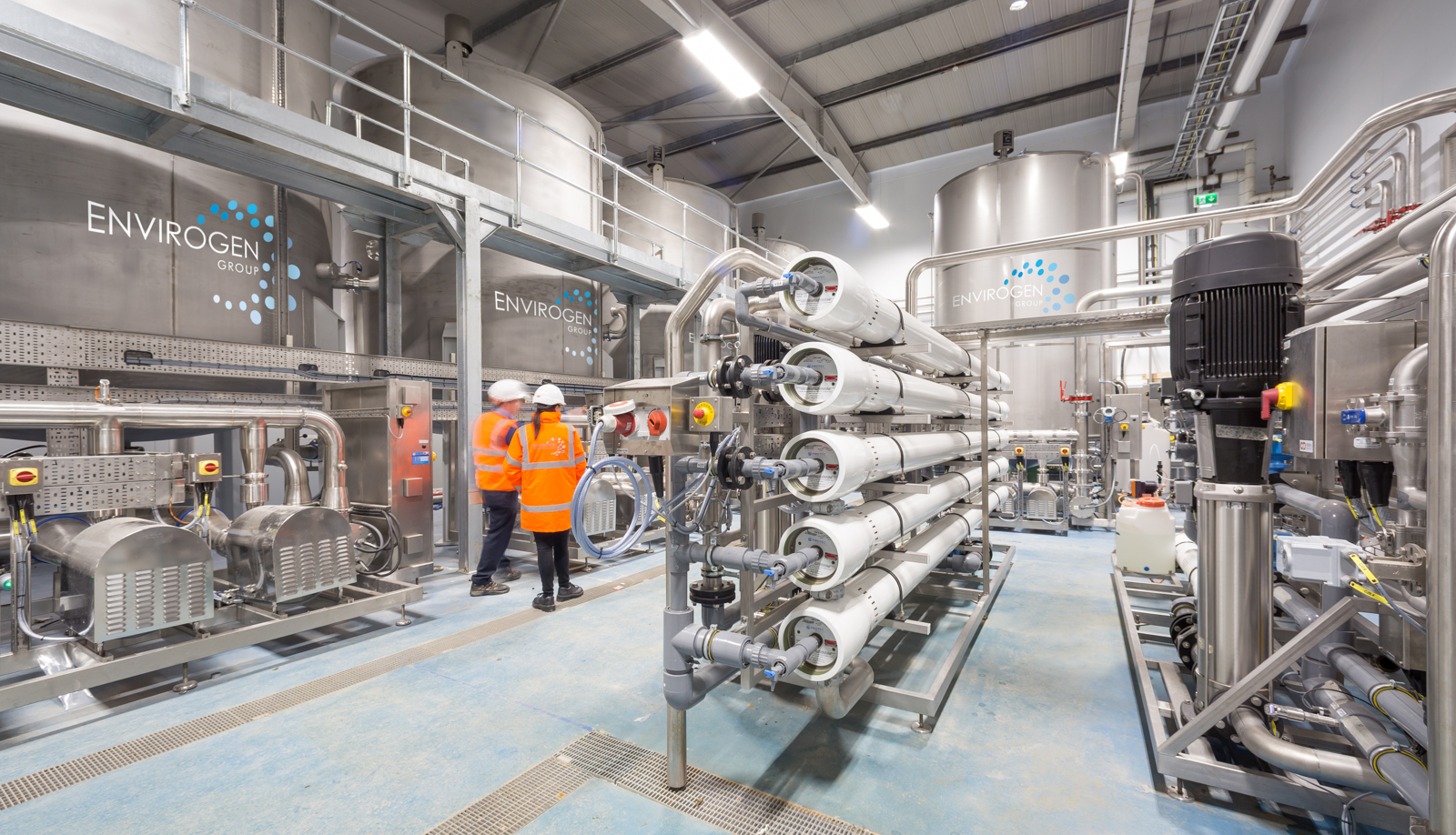
Working together to tackle the bottleneck
Envirogen were asked to provide a total solution, working through each stage of the water treatment system to recognise bottlenecks and design new processes with increased capacity. From incoming water treatment to sterilisation, and even wastewater treatment, Envirogen took a holistic approach, evaluating the needs of the site to develop the best long-term solution. This methodology has enabled Britvic to develop a programme of continuous improvement in relation to water treatment and water purification solutions. Since installing the new systems, Envirogen has continued to provide preventative maintenance services, with engineers on site, continually refining and improving systems and processes, ensuring maximum outputs are delivered to the high-quality standards demanded. The new equipment is already delivering outputs of 360m³/hour and hitting the futureproofed requirements for the site.
Integrated water purification solutions for the entire water cycle
Dealkalisation plant
As the initial stage of water treatment, a new three vessel dealkalisation plant was installed, employing ion exchange technology to remove the temporary hardness from the incoming water supply. Calcium and magnesium ions are stripped out to a rate of less than 50 ppm, meeting the rates set for all Britvic production sites and ensuring product consistency and flavour.
Following ion exchange, the water travels through a chlorination tank, to add an oxidizing agent to the water and then on to a carbon bed to the remove the chlorine. An existing ultraviolet (UV) filtration system with 10µm and 1 µm absolute cartridges, previously installed by Envirogen, destroys microbes and removes suspended solids.
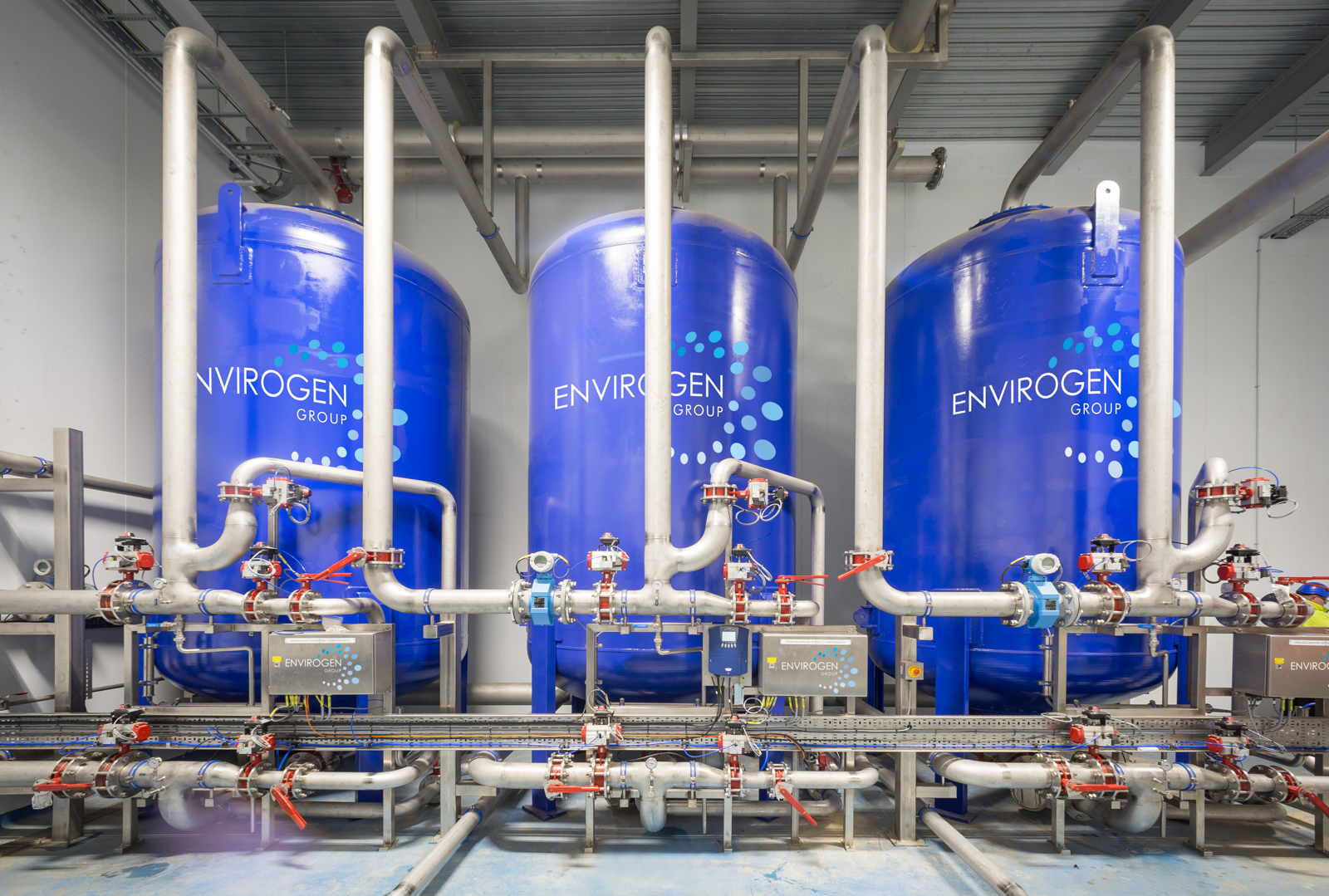
Network sterility
To maintain and ensure sterility, whilst ensuring a consistent and reliable supply of water to all areas of the site, a UV treatment tank was installed to receive water from the filtration stage. Four stainless-steel ring mains provide water across all areas of the factory, the water is kept in continual motion to maintain sterility. Take off points are provided in multiple locations to ensure that purified water is available wherever and whenever it is needed. Continuous automated monitoring ensures standards are met with water recirculated back to the UV treatment tank when needed.
Enabling Britvic’s only aseptic line
As the home for Britvic’s only aseptic/sterile, production line, the Rugby site produces long-life fruit juice products without the use of preservatives or the need for refrigeration. An aseptic line needs a more rigorous treatment protocol so Envirogen designed a reverse osmosis water purification system, or RO water purifier, to remove up to 99% of all pathogens, dissolved ions and organic compounds. Using nanofiltration to recover and recycle concentrate waste streams, Envirogen were able to achieve a market-leading 90% waste recovery rate, sending as little water as possible to drain. A feature that is helping to satisfy Britvic’s ambitious wastewater reduction targets.
Water fit for discharge
To complete the water cycle and meet discharge consent for outgoing wastewater streams, a pH correction plant was designed and installed. The site’s wastewater streams have a large pH fluctuation: with carbonation generating a low pH and caustic cleaning producing a high pH. A set of three dosing tanks were installed, each with two independent probes measuring levels and automating hydrochloric acid or caustic soda dosing. A containerised pump and control system were supplied to site, fully assembled and user acceptance tested, to ensure quick and easy connection. The entire system was constructed outside, along with the chemical stores, to conserve space within the factory and provide room for future factory expansion.
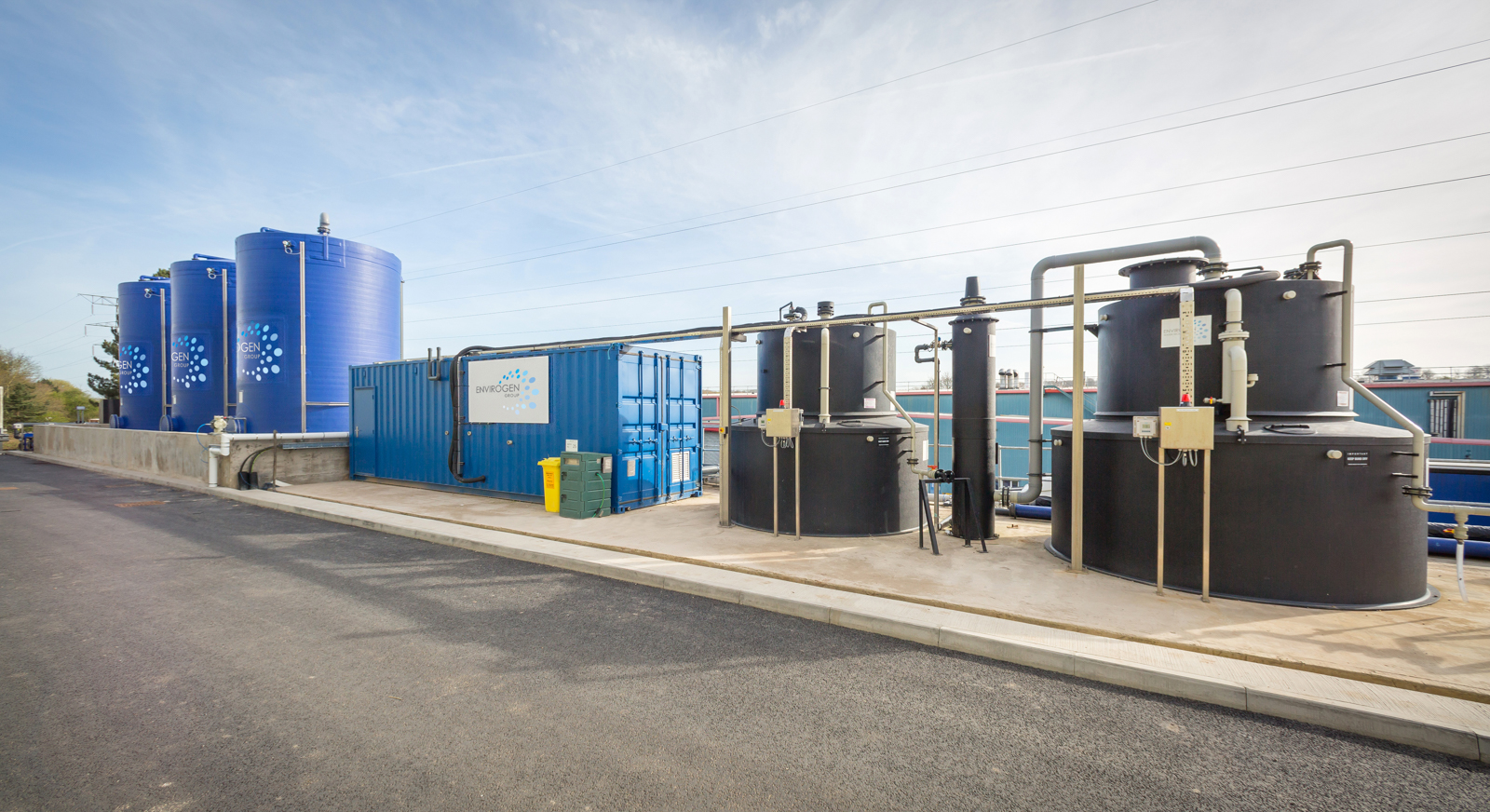
Control at every step of the journey
Automation is the key to fast and efficient soft drink manufacturing and, with the use of monitoring technology, the whole water treatment system is completely automated. To meet safety standards and to ensure quality, control and reporting are key. User-friendly control panels, located at multiple points throughout the site, provide real-time reporting, providing safety data and allowing adjustments when needed.
A holistic approach – greater than the sum of its parts
Overall, it was the holistic approach to the problem that ensured success and delivered water purification solutions that achieved more than each of their individual parts.
Denyer explains: “Each part of a water treatment system relies on the process that comes before it. To achieve the high standards that Britvic needs for their products, each step must be reliable on its own but also contribute to further efficiencies downstream. We approached the whole project with the big picture in mind. We have a clear view of the end goal and we’re constantly looking for ways to improve the efficiency of each step, whether that is to increase output, save water or cut costs.”
“Our team is used to working on complex projects of this nature. For this project, we appointed a team of designers and specialist process, mechanical and electrical engineers, as well as a dedicated project manager as the single point of contact for the client. It is our collaborative approach, both within the Envirogen team and with the client that enables us to realise the best solutions.”
“Although the new machinery reaches the futureproofed manufacturing outputs required for the site, we’re still working to reach the full main 360m³/hour site wide targets by helping Britvic to design a new chlorine dosing system that will match the increased flow from the dealkalisation step. We will continue to work with the Britvic team to help them fulfil their ambitious plans.”
Read more about Britvic water treatment and process filtration solutions:
Key outcomes
- Total water purification solutions approach delivered a system that meets the needs of the whole site
- Output on new installations increased from 200m³/hr to 360m³/, matching site wide goals for a substantial uplift in manufacturing capability
- Wastage reduced by recycling 90% of reverse osmosis discharge
- Control panels ensure full visibility and management for all systems
- A comprehensive ongoing service and preventative maintenance plan ensures that systems continue to work to full capacity
Holistic planning and design ensured that each element of the treatment supports the next and delivered a solution that is greater than the sum of its parts.
For a free assessment to evaluate water treatment and process filtration solutions for your site, contact our team of expert engineers
About the client
Britvic is a leading soft drinks company, with operations in Great Britain (GB), Ireland, France and Brazil. Britvic manufactures a range of its own brands, including Robinsons, Tango, J2O and Drench as well as PepsiCo’s soft drinks, including Pepsi and 7UP. Britvic is the largest supplier of branded soft drinks and the second largest supplier of carbonated soft drinks in GB. The Britvic Rugby factory produces half of the group’s total manufacturing output.
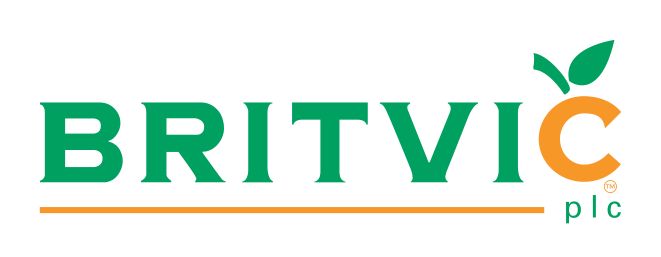